Equipment Acquisition & Preventive Maintenance for Trucking Operations
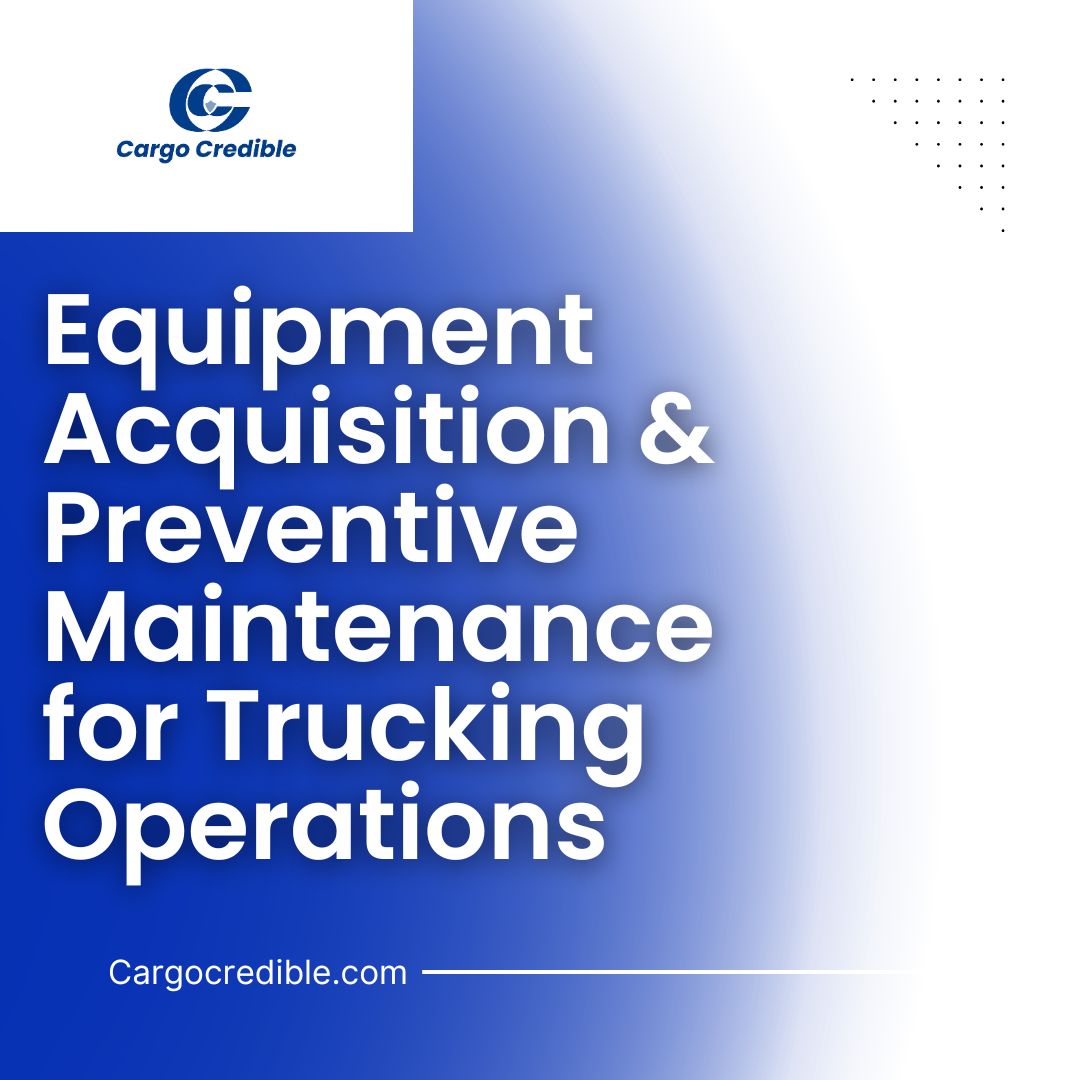
Building a Reliable, Scalable, and Compliant Fleet from the Ground Up
In trucking, your equipment is more than metal and machinery—it’s your partner on the road, your revenue generator, and your reputation rolled into one. Whether you’re a solo owner-operator or managing a multi-unit fleet, your success depends on two critical pillars: how you acquire your trucks and how well you maintain them.
Making informed decisions about your vehicles can improve operational efficiency, protect your bottom line, and keep you compliant with ever-evolving regulations. In this comprehensive guide, we’ll break down what you need to know about buying vs. leasing, selecting the right equipment, and developing a preventive maintenance program that keeps your business rolling strong.
Buying vs. Leasing: Choosing the Right Strategy
When it’s time to bring in new trucks, the first big decision is whether to buy or lease. Each path has its strengths and trade-offs, and the right choice depends on your business model, financial goals, and how you plan to scale.
Leasing: Flexibility and Simplicity
Leasing typically requires a lower upfront investment, which frees up capital to invest in other parts of your business—like hiring drivers or taking on new contracts. Most lease agreements include comprehensive maintenance packages, reducing the stress of unexpected repairs and keeping your fleet in road-ready condition.
Another big advantage? Regular upgrades. Leasing allows you to rotate newer, fuel-efficient trucks into your fleet more frequently, improving reliability and driver satisfaction.
But leasing also comes with limitations:
- Mileage restrictions and penalties for going over
- Additional charges for excessive wear and tear
- No ownership—your payments build no equity in the asset
Buying: Long-Term Control and Equity
Purchasing a truck gives you complete control. There are no mileage limits, and you can customize the vehicle to meet your specific operational needs. Over the long term, owning can be more cost-effective—especially if you run your trucks for years and maintain them well.
The challenges?
- Higher upfront cost
- You're responsible for all maintenance and repairs
- Trucks depreciate, affecting resale value
Financing Options
You don’t always need to pay cash upfront. Consider:
- Truck Loans: Traditional loans that allow you to spread costs over several years.
- Lease-to-Own: Start with lower monthly payments and gain ownership at the end of the lease term.
- OEM Financing: Offered by manufacturers like Freightliner or Peterbilt, often with competitive interest rates.
- SBA Loans: Government-backed loans for small businesses with attractive terms.
Before deciding, take a long, honest look at your projected cash flow, average miles driven, and long-term plans. Each option has its place, depending on where your business is headed.
Picking the Right Truck: Match Your Vehicle to the Mission
Buying or leasing is only the beginning. You also need the right type of truck for your operation. Two of the most important considerations are cab style and truck class.
Sleeper Cab vs. Day Cab
Day cabs are designed for short-haul routes where drivers return home each day. They’re:
- More affordable
- Lighter and more fuel-efficient
- Easier to maneuver in tight urban areas
- Cheaper to maintain, thanks to fewer systems
Sleeper cabs are built for long-haul jobs. They come with built-in sleeping quarters and often additional amenities, offering drivers:
- Comfort for overnight or multi-day trips
- Safety during rest periods
- Higher productivity on long routes
While sleeper cabs cost more and require more fuel, they’re essential for over-the-road trucking.
Class 7 vs. Class 8
Understanding truck classification is key to legal compliance and operational efficiency.
- Class 7 trucks (26,001–33,000 lbs GVWR): Used for heavy-duty deliveries within cities or for utility and refuse services. These typically require a Class B CDL.
- Class 8 trucks (33,001+ lbs GVWR): The backbone of long-haul trucking. Think tractor-trailers and heavy-duty rigs. These require a Class A CDL and are built for long distances and massive loads.
Choose the class based on the type of freight you haul, your delivery range, and licensing requirements for your drivers.
Preventive Maintenance: Keeping Your Fleet on the Road
Once your trucks are in service, keeping them running smoothly becomes your top priority. Preventive maintenance (PM) isn’t just a cost-saving strategy—it’s a safeguard against breakdowns, violations, and missed deadlines.
Build a Solid Foundation
Start with a comprehensive inventory of your equipment. For each truck, record:
- Make, model, and VIN
- Purchase or lease date
- Assigned driver(s)
- Mileage history and service records
This database will be your command center for tracking performance and planning service intervals.
Create a Maintenance Schedule
Your PM plan should combine:
- Time-based intervals (e.g., every 90 days)
- Mileage-based triggers (e.g., every 10,000 miles)
High-usage trucks may need more frequent service, while idle vehicles still require regular checkups to prevent system degradation.
Key Maintenance Areas
Focus on the systems that keep your trucks safe and roadworthy:
- Engine: Change oil, filters, check coolant and belts
- Brakes: Inspect linings, pads, drums, and fluids
- Tires: Monitor pressure, rotate regularly, and check tread depth
- Chassis: Lubricate wheel bearings and joints
- Safety components: Test lights, windshield wipers, and mirrors
Track Everything
Keep detailed records of every inspection, service, and repair. This documentation is invaluable for:
- DOT audits
- Warranty claims
- Resale or trade-in evaluations
- Internal accountability
Daily Inspections: The Front Line of Fleet Safety
Your maintenance program should be supported by strong pre-trip and post-trip inspections. These daily checkups are legally required—and they’re your best defense against roadside breakdowns or violations.
Pre-Trip Checklist
Before hitting the road, drivers should inspect:
- Brakes
- Tires and wheels
- Headlights, tail lights, and signal lights
- Fluid levels (oil, coolant, windshield washer)
- Mirrors and windshield
- Emergency equipment (fire extinguisher, triangles)
- Load security and trailer connections
Post-Trip Checklist
At the end of the day, drivers should:
- Document any issues or unusual behavior during the trip
- Report defects for follow-up repairs
- Complete a Driver Vehicle Inspection Report (DVIR) as required by law
Best Practices
- Train drivers thoroughly on what to look for and how to report it.
- Use standardized inspection forms across your fleet.
- Prioritize prompt repair of reported issues to remain audit-ready and compliant.
Paving the Road for Long-Term Success
Trucking isn’t just about moving freight—it’s about building a business that’s reliable, profitable, and sustainable. The choices you make around equipment acquisition and preventive maintenance shape every part of your operation, from safety and compliance to costs and customer satisfaction.
By investing in the right trucks, staying proactive with maintenance, and empowering your drivers to perform thorough inspections, you're laying the groundwork for a fleet that lasts—and a business that grows.
The road ahead may be unpredictable, but your operation doesn’t have to be. With a solid foundation, the right tools, and the discipline to keep everything running smoothly, you’re not just staying in the game—you’re driving it forward.
Comments (0)
- No comments yet.